Introduction
ISO 10303-209 (STEP AP209) is a standard for sharing, exchange and long term archiving of information between the iterative design and analysis stages of the product life cycle.
STEP AP209 was developed under PDES, Inc. to support the (distributed) simulation processes. A typical simulation process is provided below, identifying the several models used from CAD to study results:
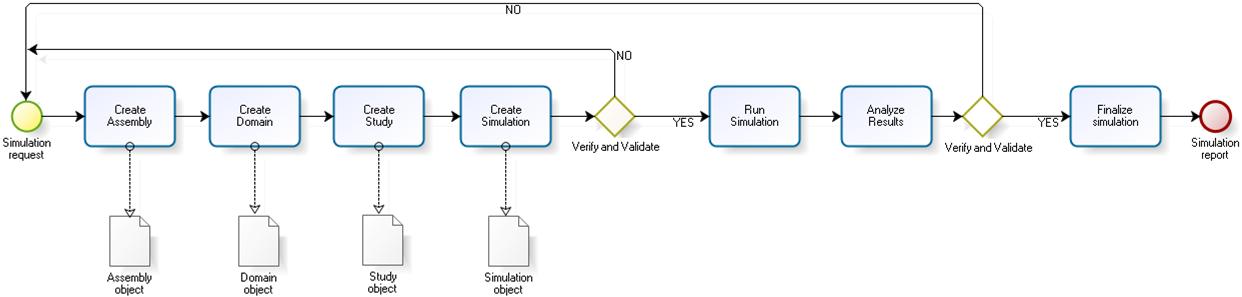
STEP AP209 was created to enable:
- Collaborative analysis and design
- To exchange engineering design and analysis data using AP209-based standard file formats between companies using different CAD and FEA systems
- Archiving of analysis and design data
- To archive configuration managed CAD and FEA data in AP209-based standard format
- To reuse that data in the future, whatever system changes have occurred
- Development of integrated systems
- To ensure that the system is not locked-in to a particular system supplier.
Scope
AP209 ed2 addresses a wide set of multi-disciplinary analysis and optimization problems.
Engineering disciplines covered today by AP209 ed2 are:
- Structural Finite Element Analysis;
- Computational Fluid Dynamics;
- Kinematics Analysis.
As introduced, the sharing of the same data model by many disciplines, as offered by AP209 ed2, is a key enabler for multi-disciplinary analysis.
More into details, AP209 edition 2 covers:
- Product definitions
- Product structure
- Including for composite structures
- The lay-up of a composite part can be specified in detail.
- Shape, stacking sequence, and property information can be supplied about individual plies and their fiber orientations.
- Product shape
- Design shape / Idealised shape
- Nodes, finite elements, their edges, faces and volumes can be explicitly associated with aspects of the product geometry.
- It is possible to specify element properties, loadings or boundary conditions on a curve, edge, surface, or volume of the geometric model.
- Structural Finite element data
- Linear static / Linear modes and frequencies
- This includes models, analysis definitions and load cases, and results.
- Computational Fluid Dynamics (CFD), mainly based upon the CGNS standard;
- Kinematics Analysis: rigid body motion, based on STEP Part 10303-105.
- Generic structured and unstructured analysis and mesh capabilities, meshless numerical analyses, developed under the European Union GEM program (Generic Engineering Analysis Model);
- Material properties
- Complete discrete/continuous mathematical field representation capability, based upon the David Taylor Labs/Boeing DT-NURBS package, to represent discrete and continuous scalar, vector and tensor fields (properties, loads, results);
- Configuration control information of above
- A version of the finite element model is linked to a version of the product.
- This ensures that the correct finite element data may be associated with the correct version of a product within a PDM (Product Data Management) system.
AP209 ed2 addresses a wide set of multi-disciplinary analysis and optimization problems.
The sharing of the same data model by many disciplines, as offered by AP209 ed2, is a key enabler for multi-disciplinary analysis.
Additional highlights
Simulation Data Management (SDM)
STEP AP209 ed2 offers capabilities to support Simulation Data Management functionalities. Under a project called Open SimDM, Lockheed Martin Aeronautics and Jotne/EPM Technologies (Norway) have developed a suite of products based on the standard using these functionalities.
Materials database
Complementing STEP AP235 (Engineering properties for product design and verification), STEP AP209 ed2 offers functions related to engineering materials database for simulation, both for composite and homogeneous (metallic) materials. Among the functionalities described in the scope of the standard, there is:
- Materials and their composition of chemical substance;
- The identification of material specifications from internal and external sources and their properties for a specific operating environment;
- Composite material structure and shape;
- The depiction of composite laminate tables describing the material, stacking sequence, ply orientation, and constituents of the composite or a portion of the composite with a defined shape;
- Catalogue data characterised by property value pairs.